硫化物系固体電解質をナノスケールでX線CT撮像 極小Φ0.5mmの超高品質試験片切り出し
東京工業大学 工学院 機械系 平井・笹部研究室
助教 博士(工学) 兒玉 学先生
東京工業大学 平井・笹部研究室様にて独自に進められている、全固体電池の材料開発の事例です。
ナノスケールレベルのX線CT撮像に求められる、極小Φ0.5㎜サイズの超精密打抜きの実現を目指し、ご相談をいただきました。
この度の事例では、同研究室助教の兒玉学先生にインタビューさせていただいた内容をお伝えいたします。
この事例のポイント
→ 良質なサンプルが安定して得られ、実験のスループットも向上!
お客様の課題
― 当社にご相談をいただく前のご課題や、お困りごとは何でしたか?
兒玉先生:弊研究室では、実験室規模CT装置ならびに大規模放射光CT装置を用いて、全固体電池のX線CT撮像を行っております。
全固体電池をナノスケール分解能でX線CT撮像するには、十分にX線が透過可能な、直径1mm以下の微小サイズのサンプルが求められます。
以前は、全固体電池シートをピンセット等で割って微小サイズの破片を作成し、それを用いてCT撮像を行っておりました。
しかしこの方法では、サンプルの品質面での問題が生じ、本来の電池構造を撮像できているのかが不明でした。また、CT像の品質も、撮像するごとに変化しておりました。
1.サンプルの作成時に、内部に亀裂が発生
品質不足のサンプルをCT撮像した結果、電池内に確認された亀裂が、本来、電池内に存在した物なのか、それとも粉砕の再に発生した物なのか、判別がつきませんでした。
2.サンプルサイズの不均一
撮像するごとにサンプルサイズが異なってしまい、CT像のクオリティーが安定しませんでした。これに伴い、1回の撮影に十時間以上を要するCT撮影の再撮影が必要であったり、仕様違いの電池のCT像の比較が困難となっておりました。クを取り扱う細かい作業は、経験を積んだ特定の作業者でなければ作業できないのが課題でした。
3.サンプルの形状が安定しない
全固体電池は大気中の水分で劣化しますので密閉治具に入れる必要があります。
直径1mm以下の微小サンプルをグローブボックスの分厚い手袋越しに密閉治具に装填するのはなかなかに難しい作業なのですが、ハンドパンチ導入以前はサンプルの形状が安定しないことにより、撮像治具内への設置のためのハンドリングも毎度試行錯誤する必要がありました。
野上技研のご提案
採用結果
― 野上技研製の治具をご採用いただいた結果はいかがでしたか?
兒玉先生:まず品質面では、直径0.5mmや1mmの微小サイズサンプルでありながら、加工に伴う亀裂を一切発生させること無く、同一形状の安定したサンプルを作成することができるようになりました。
兒玉先生:高品質の極小サンプルで撮像することにより、本来の電池構造のCT像を、同一の撮像品質で得られるようになり、作成仕様の違いによる電池構造の比較などができるようになりました。
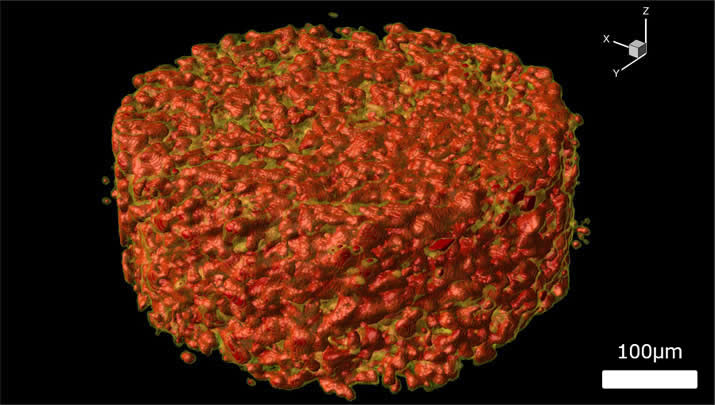
「極めて明瞭なCT像、アーチファクト(偽像)がほとんど発生せず 」(兒玉先生)
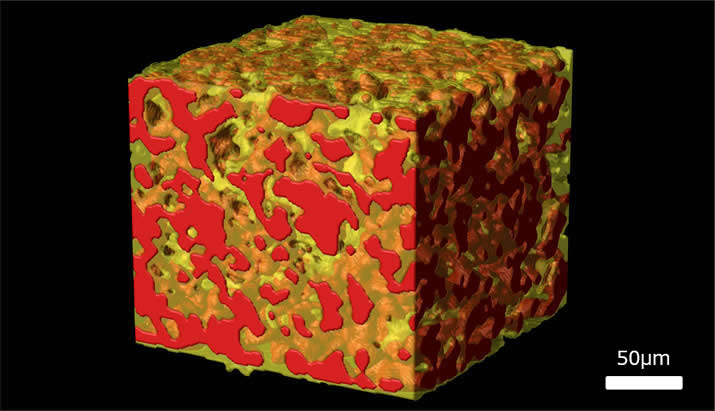
「高解像度で3次元部材分布を検討可能な良好なCT像を取得」(同上)
ご検討の過程を振り返って
― ご検討や効果検証の過程で、何かお感じになられたこと、ご印象に残っていることはありますか?
兒玉先生:野上技研様には、単に治具を作成いただくのではなく、共同研究のごとく、我々が求めた精度までハンドパンチの最適化を行っていただけました。その点が印象的です。
ハンドパンチの仕様選定(刃先形状やクリアランス設定など)の段階では、弊学まで多くの試用機と共に技術者の方にお越しいただきました。
その上で、グローブボックス内で実サンプル(シート状硫化物系全固体電池)を用いて加工テストを行い、弊研究室保有の光学顕微鏡や走査型電子顕微鏡でサンプル形状の確認を行いまして、最適なハンドパンチ仕様の選定を実施しました。
加工機一つにここまで熱心に対応いただける企業様は非常に珍しく、野上技研様の加工に対する熱意が伝わりました。
― 今後、野上技研に期待したいことはありますか?
兒玉先生:現時点でも野上技研様の加工機では全固体電池をΦ0.5mmに正確に加工できるなど、素晴らしい技術をお持ちかと思います。
そのお持ちの技術を、X線CT以外の計測や評価用に展開いただきまして、世界の電池開発に貢献いただけますと幸いです。
― この度はご多用の中、大変ありがとうございました。