SEM観察用試料 CP・イオンミリング前の精密断面二次加工
全固体電池の充放電後の劣化状況を評価する、SEM観察用サンプル作成の事例です。
充放電後のコインセルから5mm角で試料を切り出してから、CP(クロスセクションポリッシャー)にかけ、SEM観察を行います。
このCP前の切り出しの段階で、打抜き時のダメージにより断面構造が破壊されてしまい、充放電による崩壊との判別がつかない状態でした。
そのため、打抜きによるダメージがないと思われる深さまでCP加工とSEM観察を繰り返しながら評価を行わざるを得ず、「1回10時間以上」のCP加工の時間とコストが問題となっていました。
この事例のポイント
超高品質な断面が安定して得られ、SEM観察のサイクルが高速化!
お客様の課題
打抜き時の応力により断面構造が破壊
打抜きの応力により断面の破壊(割れ・崩れ・層間剝離)が起こり、充放電による劣化との判別がつかない状態でした。
加工によるダメージがないと見做せる深さまでCP加工を行う必要があり、長時間の加工を繰り返し行わざるを得ませんでした。
多層材でレーザーカットは不可 金属層ありミクロトームも不可
レーザー加工では、異なる材料の層ごとにレーザーによる変質の大きさや性質が異なり、全固体電池フルセルとしての、本来の性質を保った加工は不可能でした。
また、リチウム金属の層を含んでおり、樹脂や生体組織などの断面を加工するミクロトームも、採用できませんでした。
グローブボックス内での微小ワークの取り扱いが困難
硫化物系固体電解質は大気中の水分と反応して有害なガスが発生する為、低露点のグローブボックス内で取り扱う必要がありました。
動きが制約されるグローブボックス内で、5mm角のワークを取り扱う細かい作業をミスなく行うのは難しく、経験を積んだ特定の実験スタッフでなければ実施できないのが課題でした。
野上技研のご提案
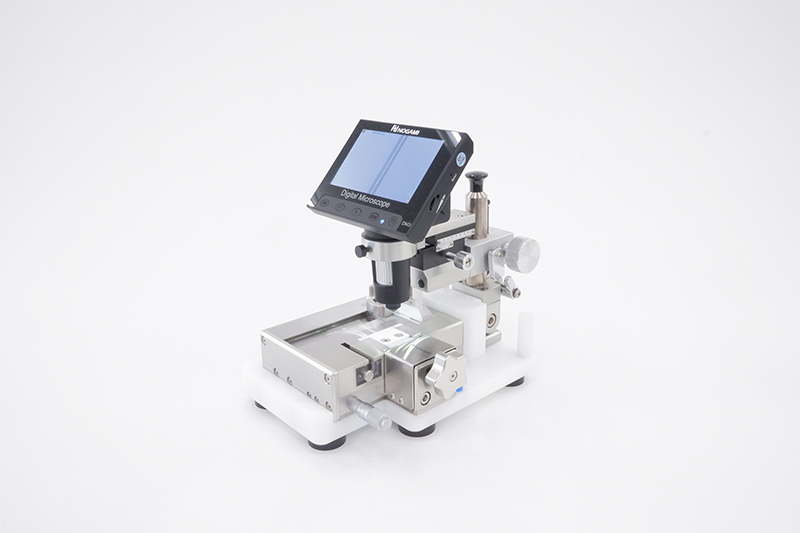
採用結果
極めて高品質な断面
サンプル打抜き後に、新たな仕上げ加工用ツールで二次加工を行う手順に変更しました。
仕上げの二次加工の結果、断面へのダメージが「まったくない」といっても良い程の、極めて高い品質の断面が得られました。
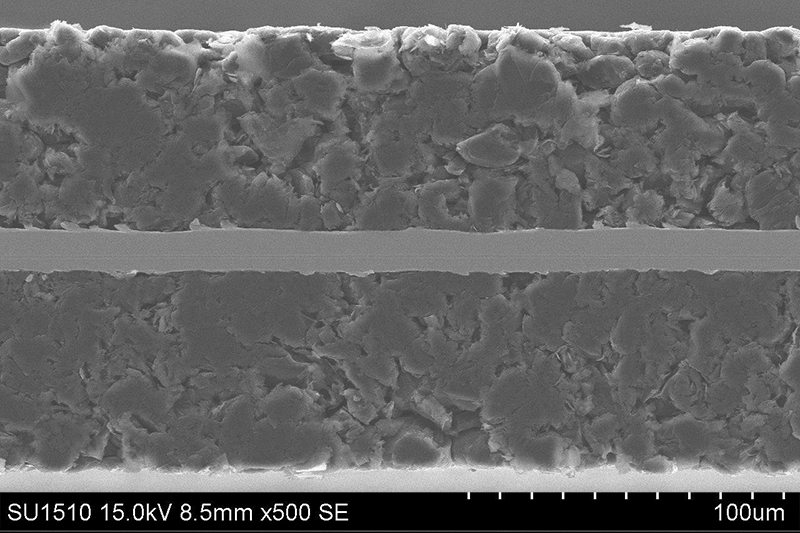
[ 写真はデモ用の負極材 1000倍で撮影]
ハンドリングのミスを予め排除する治具の使用手順と作業性
仕上げ加工用ツールへの試料のセット~加工、材料の取り出しまでの手順は、その後の取り回しも含めて、細かな工夫が施してあります。
狭いグローブボックス内で、手に大きなグローブを付けた状態でも、誰もが最小の手数で、ミスなく、スピーディーに作業できる様になりました。
SEM観察前のCP加工深さは 100μm 以下に、回数も1回だけに
サンプル加工時の応力による断面へのダメージが無い深さまでCP加工する、といった工程が実質的に不要になりました。
CP加工の本来の目的である、SEM観察前の試料界面の最後の仕上げのみ、1回だけで済みます。コスト低減と同時に、観察結果の信頼性も大きく向上しました。